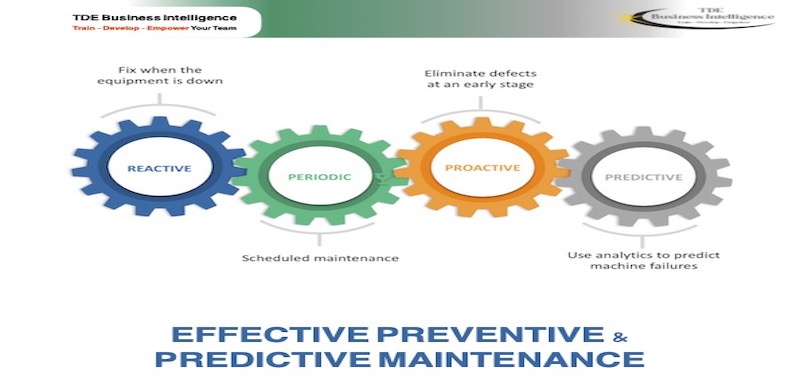
SCHEDULE
Dates | Venue | Category |
7-11 August 2023 | Port Moresby – Papua New Guinea | Maintenance-Technical |
21-25 August 2023 | Kuala Lumpur – Malaysia | Maintenance-Technical |
9-13 October 2023 | Bangkok – Thailand | Maintenance-Technical |
INTRODUCTION
This Effective Preventive & Predictive Maintenance training seminar will present a detailed overview of refining process yields, from the crude oil feed to the finished products. It is targeted at personnel directly involved in refining utilization and optimization, including but not limited to refining technologists and operations personnel as well as non-technical personnel interested in these processes or involved in refinery planning.
All the major refining processes are explored and examined with a view of understanding and appreciating how each unit relates to each other whilst at the same, time how these relationships can enhance refinery operations. Major refining processes are presented and discussed, including feedstock, feedstock preparation, operating conditions, catalysts, product properties and refinery yields. Refining economics will be included as means to optimizing refining operations and profitability.
The Effective Preventive & Predictive Maintenance training seminar is oriented toward the practical aspects of refinery operations and yield optimization and includes the terminology used in the industry.
BENEFITS OF ATTENDING
Upon the completion of this training, participants will be able to:
- Understand how world-class organizations solve common planning problems
- Improve productivity through use of better, more timely information
- Implement a practical and effective predictive maintenance effort
- Improve consistency and reliability of asset information
- Optimize preventive and predictive maintenance strategies
WHO SHOULD ATTEND?
- Maintenance Managers & Supervisors
- Personnel designated as planners, or identified to become planners
- Predictive Maintenance Technicians & Supervisors
- Key Leaders from each Maintenance craft
- Maintenance & Reliability Engineers
- Materials Management Managers / Supervisors
- CMMS Key Users
COURSE OUTLINE
Session 1: The Need for Maintenance
- Maintenance & Asset Management as a Business Process
- Risk Based Maintenance (RBM)
- Causes of Failure
- Likelihood & Severity of Failure – Risk Analysis
- Failure Mode Effect & Criticality Analysis (FMECA)
- Choosing the (preventive) Maintenance Tasks
- Optimization of Maintenance Decisions
- Failure Pattern Identification
- Statistical Analysis of Failures
- Weibull Analysis
- Zero Base Budgeting
- Define the Production Requirement
- Define the Maintenance Requirement
Session 2: Developing the CMMS
- Database & Structure
- CMMS & Workflow
- CMMS & Maintenance Strategies
- Asset Register
- Configuration Management
Session 3: The Planning Function
- The Maintenance Workflow and How It Relates to the Preventive Maintenance Strategy
- Roles & Responsibilities in Work Preparation, Planning and Scheduling
- Principles of Work Preparation & Planning
- Principles of Scheduling
- Network Planning
Session 4: Predictive Maintenance
- Potential Failure Analysis (PFA)
- Integration of PFA with FMECA & RBM
- Understanding the P-F Interval
- Decide which Technologies to Apply
- Predictive Maintenance Technologies
- Vibration Analysis
- Visual Inspection
- Infrared Thermography
- Temperature Sensitive Labels
- Megger Tests
- Ultrasonics
- Oil Analysis
Session 5: Control of the Maintenance Process
- Implementation Stages of Preventive & Predictive Maintenance Strategies
- CMMS Integration
- Reporting – Use of (Key) Performance Indicators
- Case Study