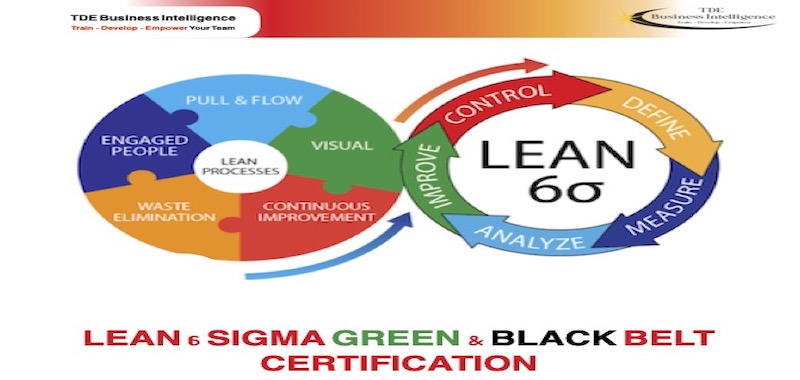
SCHEDULE
Dates | Venue | Category |
13-16 February 2023 | Bangkok – Thailand | Quality |
29 May-2 June 2023 | Kuala Lumpur – Malaysia | Quality |
21-24 August 2023 | Port Moresby – Papua New Guinea | Quality |
INTRODUCTION
This Lean Six Sigma Boot Camp is time-proven to impact your professional skill set and enhance organisational effectiveness. The learning objective of this high impact program of business excellence is to develop a comprehensive set of skills that facilitates effective functioning of a Six Sigma green/black belt. The established body of knowledge includes techniques for both quantitative and non-quantitative analysis, as well as requisite team leadership skills necessary to institute high impact Six Sigma deployment. This boot camp skill-fully blends world class concepts of success along with empowerment techniques.
TOP LEARNING OBJECTIVES
- TRANSLATE proven six sigma models to laser-focused business objectives and targets.
- TRANSMIT Six Sigma concepts within the organisation for forward thinking standards.
- TRANSFORM your professional performance as a collection of up-to-date processes, with inputs to resolve operational challenges in the most expedient approach.
- FACILITATE skilful application of the DMAIC process sequence as a basis to organize process enhancement.
- EXPAND your professional process improvement techniques to enhance organizational effectiveness.
- ELIMINATE guesswork! Manage the data-driven concept of a Six Sigma quality levels to evaluate process capability within your organization.
- RECOGNIZE the organizational factors that are necessary groundwork for a successful Six Sigma effort.
BENEFITS OF ATTENDING
- HIGH IMPACT PROCESS EXCELLENCE – Six Sigma methodology focuses on customer awareness and subsequent business improvement. In addition to reducing the process defects, six sigma methods facilitate improvement through world class channels. Subsequently, that means identifying and remedying problems wherever they occur. It pinpoints anything that damages business functionality in a way that increases defects, raises costs, slows productivity or reduces customer satisfaction in a source of variation. The Lean Six Sigma Boot Camp seeks to eliminate or remediate these sources to facilitate overall business improvement.
- REDUCING PROCESS VARIATION – Process defects can irrevocably harm customer satisfaction levels, as each customer becomes a potential lost consumer. Subsequently they tend to pass the word about product defectives. Even the best products and services can be ruined by failing to identify and correct the process variation.
- REDUCING OPERATIONAL COSTS – The Lean Six Sigma Boot Camp integrates two recognized winning strategies: Six Sigma and Lean Operational Processing; whether it be manufacturing, business strategy or administrative functions. This integration results in the ability to identify process waste and reduce defects, operational variations and mistakes. We focus on inventory reduction, more effective labor utilization and strategies to enhance business success whether it be manufacturing or transactional functions.
- CYCLE TIME COMPRESSION – Any decrease in process cycle time or service performance strategy means costs savings, reduced maintenance expenditures and lower payroll burden. Customer satisfaction ratings skyrocket when we reduce process time and increase service quality level. The Lean Six Sigma Boot Camp focuses sharply on these goals.
- ENHANCE CUSTOMER SATISFACTION – The Lean Six Sigma Boot Camp is laser-focused on three levels of customers; business level, operational level and process level. Customer satisfaction is an objective all its own. Each aspect of a business’ operation, from marketing strategies to sales personnel performance, has a positive or negative affect on customer satisfaction. The sources of variation that Six Sigma corrects is a sure-fire cure to inherent operational issues.
WHO SHOULD ATTEND?
Management Professionals (those responsible or keen to bring visible breakthrough improvements in key processes) who wants to achieve operational excellence in the organization. Some departments will include:
- Plant and Asset
- Manufacturing and Operations
- Project Management
- Process Control & Production
- QC/QA
- Business Development & Strategic Planning
- Construction
- Customer Service
- Sales & Marketing
- Information Technology
- Human Resources
- Finance and Accounting
- Technical & Engineering
Management From The Following Industries:
- Power and Utilities
- Construction
- BPO
- Manufacturing
- Oil and Gas
- Banking and Finance
- Retail and Hospitality
- Service
- Shipping and Logistics
- Petrochemical
- Healthcare
- Agriculture & Commodities
- Government
- FMCG
- Telecoms
- Food & Beverage
- IT
COURSE OUTLINE
LEAN SIX SIGMA SKILL POINTS
GREEN BELT CERTIFICATION
DAY 1: POWER-UP TODAY’S BUSINESS WITH LEAN SIX SIGMA
- Concepts and history of winning strategic thinking… the best of the best: Benchmarking
- “Speed and Accuracy” blending lean process and six sigma
- Kano analysis; three levels of customer responsiveness
- Winning business metrics…VoC & CTQ; the concept of “Value Added”
- Six-Sigma; the process & the people… a study in human interaction and team dynamics
- Conventional six sigma…transactional six sigma; functionality in business applications
- The foundation of six sigma methodology; DMAIC sequence protocol
- Project team considerations… selection of specific team members/SME
- Project template application: understanding project deliverables; a concise game plan
- Quality function deployment (QFD) for business operations; forward thinking six sigma
- Project identification and the problem statement…beginning six-sigma with a clear focus
- DMAIC methodology…understanding the project charter; Writing the business case
- Applying the concepts: COPQ & CODND; funds returned to working capital
- Attribute & Variable data…discrete & continuous data; what we count… what we measure
- Data Sets: mean, median & mode; identification of outliers and data skew
- Data sets & histograms; frequency distributions, normal distribution
- Standard deviation…what’s a sigma and why do we want six of them?
- Standardized scores…Z tables as applied to six sigma
- Descriptive and inferential statistics…knowing when to use what
- Beginning our six sigma class project; the define phase
Using the case study of workplace turnover reduction in commercial banking
DAY 2: DATA-DRIVEN SIX SIGMA CONCEPTS
- Data Validation: MSA: measurement system analysis… Gage R& R
- Graphing discrete & continuous data; software interface
- Laser-focused insight of variation; common cause variation/special cause variation
- The concept of process capability, 1 ½ ó drift
- Working within customer specification limits: LCL & UCL
- Microsoft Excel & Minitab statistical software applications
- Process tolerance; understanding process capability: Cp & Cpk
- Process Analysis…Y= f(x)-Identification of key process input variables
- Using the SIPOC diagram for process analysis…the strategic view of business
- Process mapping: levels I, II & III
- Cause & effect diagrams: Ishikawa/fishbone chart analysis
- Brainstorming process…a study in human dynamics; “groupthink”
- Regression Analysis: an analytical tool; correlation, covariance and r2 values
- Application of the “Five Whys”
- Working with our six sigma project: applying metrics to six sigma methodology
- Improve phase of six sigma; Kaizen application
- Pareto 80/20…it works every time
- Control Plans: lock in the learning with metrics and procedures
- Poka-yoke six sigma applications; understanding prevention, detection & mitigation
- Working with
FMEA as a prevention tool; case study of hospital operating costs reduction
DAY 3: BLENDING LEAN BUSINESS PRINCIPLES TO SIX SIGMA
- Integration of lean tools into the six sigma project function
- Lean processing/lean manufacturing/lean office; principles & history
- The Toyota Production System in action
- Process speed from RFQ to fulfillment
- Blending customer-driven systems into our business; deployment of the pull systems
- Identifying seven types of process wastes
- Basic workplace organization and layout
- 5S concepts to all applications of operations; professional workplace organization
- Visual management; making employees a part of the process
- Identifying and eliminating workplace duplication: right- size organizational awareness
- Process simplification: An awareness of process complexity and employee fatigue
- Build in process stability/predictability: Avoid workplace inconsistency
- High Level green process integration; protecting our planet
- Employee involvement: empowerment; the Power of Kaizen Events
- Completion of our green belt class project; project team report
- Six sigma Review: Q & A
- Completion of the Lean Six Sigma Green Belt Certification
The case study of improved process changeover for increased efficiency
Advanced LEAN SIX SIGMA SKILL POINTS
BLACK BELT CERTIFICATION
DAY 4: FORWARD-THINKING CONCEPTS OF BUSINESS
- Integrating advanced six sigma tools into our class project
- The blueprint of Lean Enterprise
- Forward-thinking concepts of workplace simplification
- Quality at the source
- Process standardization across the business
- Supply chain acceleration; vendor partnerships
- Value Stream visualization… current state… future state visualization
- Applying the Theory of Constraints
- Process balance/load-leveling design for effectiveness
- TAKT time synchronization; customer-driven process speed
- Integrating the Theory of Constraints for effectiveness
- SMED; rapid response system changeovers
- Point of use supplies for speed
- Controlling office inventory: Kanban principles and application
- RTY calculations…a true measure of efficiency
- Quality at the Source…eliminate the need for quality checks
- Making the most of time; SMED application in the workplace
- Cellular work model; cellular processing
- FMEA as a prevention tool; a class work project,
- Black belt project integration
APPLYING INFERENTIAL STATISTICS TO SIX SIGMA
- Good statistics/bad data…the critical basis for data validation
- Descriptive statistics…inferential statistics; when to use what
- Population & sample data; ó& μ, X bar& s; understanding the applications
- Working with the Central limit theorem
- Populations <30; Student’s “t-tests”, statistical degrees of freedom; n-1
- Hypothesis testing for the mean; Ho & HA
- Calculating and applying the acceptance region & critical value
- Confidence intervals
- Understanding Type I& Type II errors; α& ß risks
- Process Improvement Design…Class Exercise
- Lean Six sigma concept wrap up… summary of skill points
- Completion of six sigma class project work; project team report
- Completion of the Lean Six Sigma Black Belt Certification