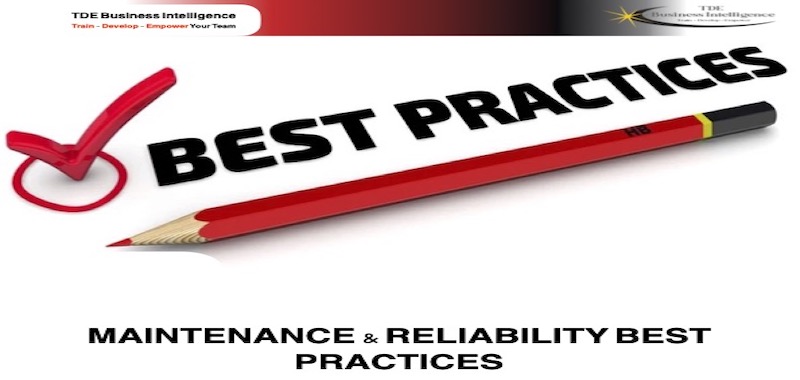
SCHEDULE
Dates | Venue | Category |
18-22 June 2023 | Dubai – United Arab Emirates | Maintenance-Technical |
INTRODUCTION
Lower revenues due to lower commodity prices have placed equipment life-cycle costs under the management spotlight like never before. Maintainers are faced with the challenge to deliver the same levels of equipment safety, reliability and availability with smaller budgets.
This Maintenance Engineering training seminar on Maintenance & Reliability Best Practices introduces the practical tools and practices that organisations need to adopt to drive down their equipment life-cycle costs in practical ways.
This Maintenance Engineering training seminar emphasizes the most effective strategies, policies, tactics and practices that are needed to ensure the reliability, integrity and durability of the physical assets through their life-cycle.
BENEFITS OF ATTENDING
Upon the completion of this training, participants will be able to:
- Understand the concepts of costs, capital, profit and ROI
- Understand the cost impact of unanticipated failure
- Apply proactive policies to reduce future maintenance costs
- Structure and analyse failure data to reduce repetitive failures
- Identify root causes of unanticipated failure costs
- Reduce resource costs through efficient work management practices
WHO SHOULD ATTEND?
- Maintenance Managers & Supervisors
- Personnel designated as planners, or identified to become planners
- Predictive Maintenance Technicians & Supervisors
- Key Leaders from each Maintenance craft
- Maintenance & Reliability Engineers
- Materials Management Managers / Supervisors
- CMMS Key Users
COURSE OUTLINE
Session 1: Equipment Life-cycle Cost Introduction
- Definitions of Reliability, Maintenance & Asset Management
- The Concept of Costs, Capital, Profits and Return On Investment
- The Asset Healthcare Model
- Key Areas of Asset Management
- Open Discussion Sessions
Session 2: Cost Factors and Causes
- The Real Cost of Unanticipated Failure
- Asset Performance Standards
- The Forms of Asset Failure and Degradation
- The Causes and Nature of Asset Failure and Degradation
- The Effects, Cost and Risks of Asset Degradation
Session 3: Breaking the Cycle of Degradation and Costs
- Programmed Maintenance
- Programmed Maintenance Intervals
- Condition-based Maintenance Intervals
- Implementing Optimised PM Programs
- Optimizing Spares to Support the Maintenance Program
Session 4: Cost Reduction through Defect Elimination
- Failure Data Collection and Analysis
- The Impact of Chronic Failures vs. Intermittent Failures
- Focus Improvement through Pareto Analysis
- Quantify losses in Life Cycle Terms
- Rigorous Root Cause Analysis Techniques
- Discussion of Software and Templates to Support Analysis
Session 5: Work Management converts Strategy to Practice
- Work Identification and Defect Reporting
- The Importance of Backlog
- Planning for Quality and Reliability
- Capacity Planning
- Scheduling for Efficiency
- Work Logistics and Preparation
- Checklists and Practical Aspects Work Quality Control
- Final Discussion and Evaluation